The modern economy is an economy of high technology and high competition. The success of business in today’s realities largely depends on how much the company is able to meet the level of rapid technological development to withstand competition. That is why today the question of when to begin changes in the company to ensure such compliance is no longer relevant. The question is how to organize and effectively manage changes so that they are continuous improvements and ensure success in a highly competitive environment. On the other hand, the coronavirus pandemic that broke out all over the planet showed how vulnerable the modern economy still is and how susceptible it is to crisis phenomena. In the crisis era the role of change management is extremely important, because sometimes only adequate, rapid and effective changes can save the business and ensure its sustainability. Therefore, based on the fact that the change management at the current stage is a necessary tool for the company, and also taking into account the total and rapid introduction of high technologies, it should be stated that the modern change management should be based on innovative technologies, which provide the company with the possibility of choosing the most relevant changes and their rapid and effective implementation. And if we consider companies engaged in operational activities – industrial, logistics, service, etc., then, taking into account the introduction of a new technological mode – Industry 4.0, change management in such companies can be carried out only on a digital technological platform.
Digital twin – a change management platform in Industry 4.0.
The optimal technological platform for change management in Industry 4.0 is the creation and application of digital twins of the company.
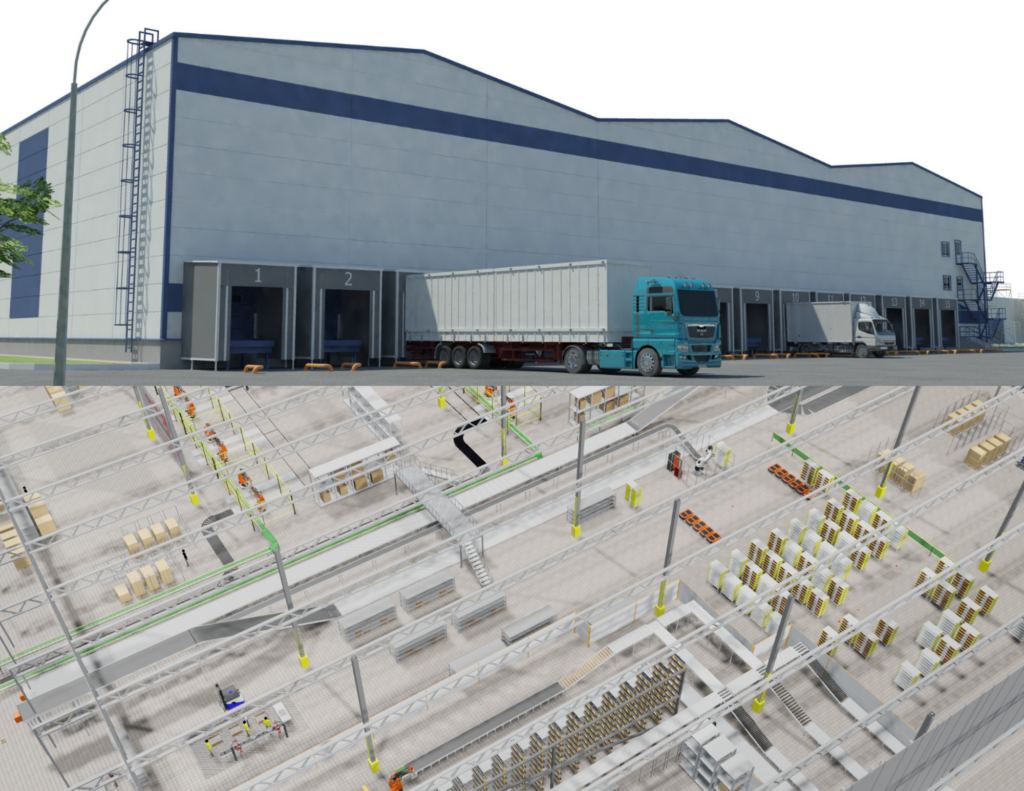
Digital twin of the operating activities of the enterprise is a computer 3D simulation dynamic model of the operational processes occurring in the company. The use of digital twin allows the creation (engineering), modernization (re-engineering) and operation (management) of processes to carry out in a model-driven mode, which enables change management, based on multi-criteria optimization throughout the life cycle of the company.
Digital change management at all stages of the enterprise life cycle. It is very important that the use of digital twins is appropriate for change management at all stages of the life cycle of the company – from the idea of its creation, including the stages of designing buildings and structures, equipment selection, technology implementation and organization of operations, project, process and other management, optimization of capacity and asset use, controlling, as well as the stages of restructuring, modernization, transformation, etc.
Managing technological change and transformation
Industry 4.0 involves the maximum use of automation and robotics. The design, operation, and modernization of such production, logistics, and other facilities involve complex change management, which is sometimes simply impossible except in the environment of digital twins.
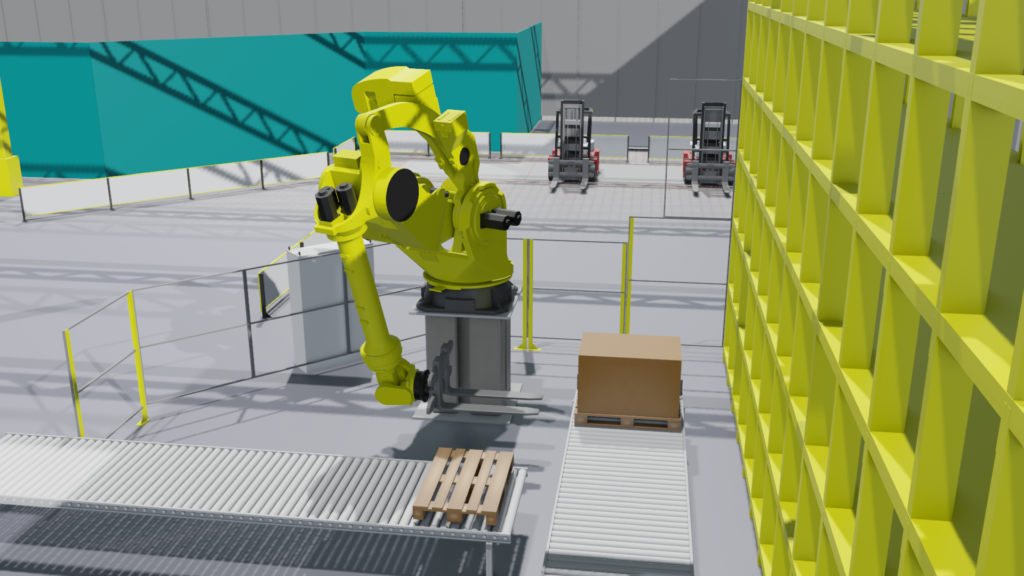
When designing industrial facilities of this level of complexity, engineers face the need for regular change management, which is most effectively implemented in the environment of the digital twin, because only there is an opportunity to analyze, using 3D dynamic simulation, the different options of choice of technological equipment and, depending on the choice made, to optimize possible layouts, depending on changes in the range of manufactured products. Directly in the digital twin it is possible to collect digital analytics on the productivity, depending on the changes in the designed processes, rhythm and tact of the production output, etc. Also the most important advantage of using digital twins for change management of the existing enterprise is an increase in the speed of implementation of technological change, as in the digital twin can be simulated and debugged not only the change itself, for example, the work of modernized production equipment, but also the project (set of processes) technological transformation – the transition from the current to the new state of the enterprise.
Organizational Change Management
The concept of continuous improvement, which ensures the competitiveness of modern business for Industry 4.0 and in terms of the organization of operational activities, is also based on a model-regulated approach, using digital technology. In the environment of digital twins, organizational innovations such as the implementation of scientific work organization, lean production (LeanSixSigma), process management and many others can be optimized.
The introduction of organizational innovations is largely associated with tests and experiments, in which the processes of the company are changed and the required parameters are optimized. Such optimization, and multicriteria, in the best way and is carried out with the use of simulation in the environment of digital twins, which provides maximum efficiency to the process of organizational change.
Management of anti-crisis changes
One of the varieties of changes are anti-crisis changes. These changes are carried out in a company during a crisis, which may be caused by both internal and external factors. The purpose of anti-crisis changes can be either to eliminate or minimize the impact of adverse factors that have a negative impact on the company, or to find other solutions, such as re-profiling the business, that can get the business out of the crisis. Anti-crisis changes, as a rule, are characterized by the fact that they are implemented under conditions of limited resources – time, financial, etc., and, therefore, the choice of adequate solutions at the stage of anti-crisis changes is very important. “The right to make a mistake” at this stage may no longer exist. In this regard, the role of digital technologies in the development of anti-crisis plans is extremely high
Digital twins of the company’s operations are an effective tool for the development, planning and justification of anti-crisis changes, as they allow you to quickly simulate different scenarios of impact on the crisis situation, to make estimates of the impact of the considered measures on the impact of crisis phenomena, to make a risk analysis and choose the best solutions. Change management and risk management can be integrated in a digital environment. A relevant example of using digital twins for crisis management changes can be simulation in digital twins of the company’s operations during the COVID-19 coronavirus pandemic, when under the influence of the pandemic some personnel are sick or self-isolated, and sanitary and epidemiological standards come into effect, which require, in particular, distancing when operators work.
Management of marketing changes
The need for changes at the present stage in many companies arises due to the rapid pace of changes in the market. That is why the guarantee of company’s competitiveness is the adequate conformity to market trends. And industrial leaders themselves initiate such changes which lead to the birth of new market trends. In the environment of digital twins, it is possible to plan and manage the changes of the company which are connected with the changes of the market. As an example of using digital twins in the company Unilever-global leader in the industry of consumer goods-foods and household chemicals. The company’s products (such as ice cream, teas, deodorants, etc.) are seriously exposed to market changes associated with frequently changing market preferences of customers, changes in seasonal demand, with differences for men’s and women’s product lines, etc. Unilever uses digital twins to quickly simulate and optimize the reconfiguration of its production lines, based on marketing analysts’ forecasts of changes in demand for its products in the market.
Change Management in VR/AR
Today’s digital doppelgangers can be handled not only on the computer, but also in a virtual and augmented reality (VR/AR) environment, which opens new horizons for change managers and brings changes to many traditional processes. For example, you can change the industrial equipment sales process by doing a VR demonstration of the equipment being sold to the customer, showing and coordinating in VR the customer-oriented custom refinements before they are actually done. Or, for example, to radically change the process of training to work on the same industrial equipment or maintenance of that equipment, when the actual expensive equipment in order to learn how to work on it or how to maintain it is not required. All that is required is a digital twin, which can be operated in the VR environment, and knowledge can be acquired through specially created AR training courses. The cost of such a learning process is an order of magnitude lower, and the knowledge obtained is comparable.
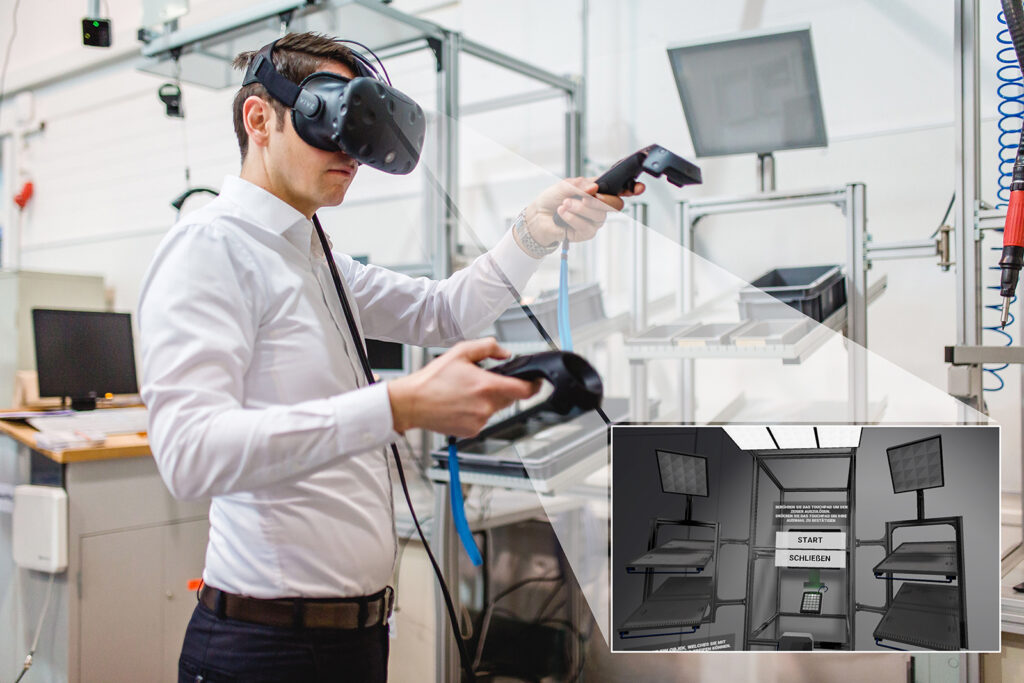
Collaborative change management
Today, the slogan is quite valid: change is life! Indeed, if a company does not change quickly to ensure its competitiveness, there is a chance that the market will go far ahead and leave the company completely “out of business”. There are many sad examples of this, including the disappearance from the market of significant and large, in the very near past, players. And the speed of introduction of changes becomes a critical parameter that ensures market success.
To accelerate the implementation of changes, of course, you can’t do without modern digital technologies – remote communications, engagement tools, collaborative project work, and so on. Modern advanced software products for working with digital twins support exactly such technologies – they work on all types of digital devices, allow collaborative group work on projects, provide each group of users with the necessary information – design and technological, analytical, visual, reporting, etc. Thus, collaborative management of changes, comprehensive development of changes, involvement of employees in the innovation process is provided, and thereby the acceleration of change implementation is achieved.
Management of efficiency of changes
But quick changes are not enough. Sometimes ill-conceived changes lead to no less disastrous consequences than delaying their launch. Change must be both quick and effective! In digital twins, it is possible to provide Model Driven Change Management, where change management decisions are applied based on their scenario modeling in a digital environment based on the analysis of required parameters and KPIs.
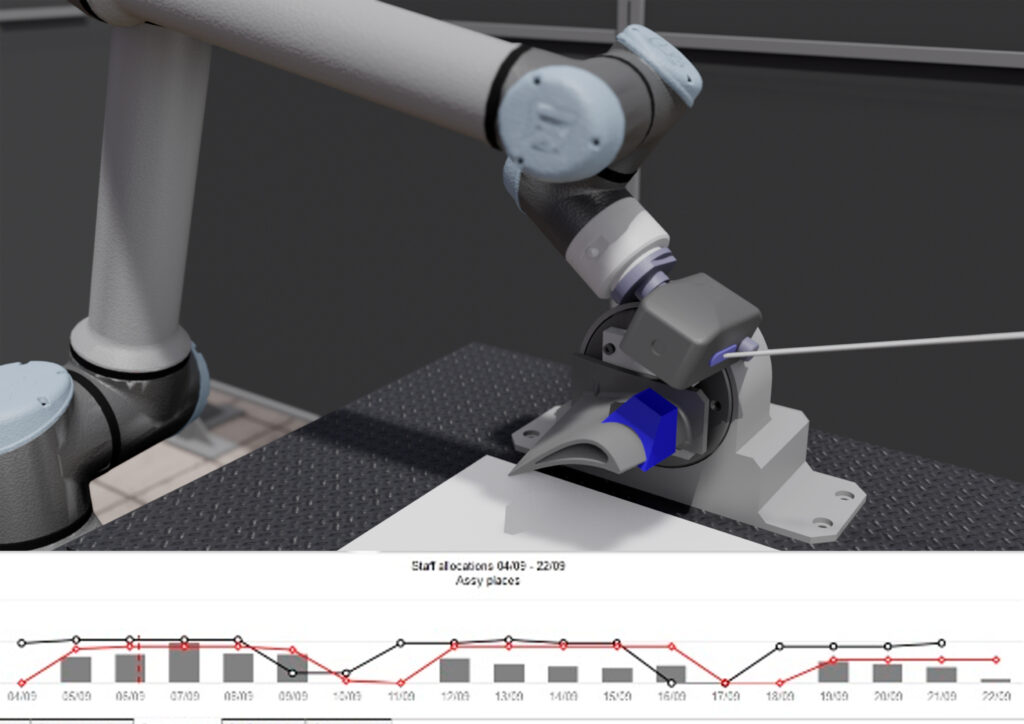
Managing Strategic Change
Strategic change may have been a good place to start when reviewing the functionality of digital change management, but it’s clear that strategic change management is where it needs to end. Change management, like other areas of management, implements the classic Plan, Act, Control, Analyze (PDCA management cycle). The end of each turn of this cycle is associated with an analysis of the current situation, and the beginning of a new cycle – with the development of strategies for the next change. Companies possessing and effectively using digital twins and their above capabilities, collect unique digital data (Big Data), on the basis of which, in the digital twins can be optimized programs and projects of further strategic business transformations, including taking into account the analysis of statistics and probabilistic forecasting. Leading consulting companies in the field of strategic management offer, for example, adapted tools for strategy deployment, using analysis in digital twins – in particular, Digital Hoshin Kanri.This methodology equips the company with a digital tool and step-by-step roadmap, which ensure subordination of all subsequent changes to a single strategic goal setting and digital control of strategy compliance at all hierarchical levels of the company.
Agile technologies of digital change management systems implementation
If talking about the most rational methodology of modern digital change management system implementation in a company, the consulting companies which implement software for working with digital twins, recommend using Agile technologies and process approach – this will help systematize and formalize the change processes in the company and their management, apply rapid sprints for implementing changes, and based on model-adjusted analysis and management of their effectiveness
Instead of a conclusion: change is life!
Modern life is full of changes. And modern life is more and more digital life! Use modern digital technologies that will allow you and your companies to change for the better!